First of
all, while it is possible to do nicropressing by yourself, it is a lot
easier if you have someone helping. The tool takes both hands to crimp
and that leaves none for holding the work to be crimped. My West Marine
store has a work bench available that has the crimping tool mounted to
the bench, so to crimp, you only have to move one of the handles. Check
with yours.
Anyway, check the crimping tool. The one I used had three holes
(crimping positions) I believe the three positions correspond to the
size of wire (fittings) you are working with. (Someone correct me, if I
am wrong. For the 1/8 inch cable I think I remember using the center
hole. The holes are machined on one side. Align the tool using the side
without the machining.
I recommend you use two sleeves for each eye you plan to make. Also
decide whether or not you plan to put a thimble in the eye.
Thread one end of the wire through one side of the sleeve and then back
through the other side to form a loop in the end of the wire. Make sure
to wrap the end of the cable with just one or two wraps of masking tape
to keep the end of the cable from unlaying.
I like to leave about 1.5 - 2 inches of the cable sticking out of the
first sleeve. If you plan to use a thimble, cut the little points off
the thimble with a good pair of wire cutters. Insert the thimble into
the loop. Put the first sleeve into the tool so that round sides are
held in the curved part of the hole in the tool, with the flat side
mentioned above, flush with the side of the sleeve closest to the
thimble. Close the tool just enough to firmly grasp the sleeve without
compressing it. Pull the wire carefully so that the loop tightens around
the thimble. While holding the loop tight, compress the end of the
sleeve by completly closing the tool. If you have done it correctly the
sleeve will be tightly up against the small end of the thimble with no
ridge around the end of the sleeve.
Turn the tool over or flip the sleeve over in the bench tool. Crimp the
center of the sleeve by closing the tool fully. Make the third crimp at
the end of the sleeve away from the loop. Its end should also be smooth
without a ridge on the end. (Align the sleeve in the tool so that the
end is flush with the side of the tool.
You have completed crimping the first sleeve. Slide the second sleeve
onto the wires toward the loop and the first sleeve. Push it up against
the first sleeve. Mark the wire short end with a Sharpie. Make the mark
one cable diameter outside the second sleeve (1/8 inch) if you are using
that size cable. (As you compress the sleeve, it expands along the
cable. The idea is for the end of the cable to be flush with the end of
the wire after three crimps are made in the sleeve.) Slide the second
thimble away from the first until it is off the short end of the cable.
Wrap the cable with a little masking tape to prevent the cable from
unlaying. Place the tape on the cable so that the mark is not covered.
Cut the cable (SHORT END!!!) at the mark with a good quality cable
cutter. Slide the second sleeve back against the first and crimp as
described above, starting at the inside end. If you have done it right,
the end of the second sleeve will be flush with the end of the short
part of the cable.
When you put a loop on the other end of the cable, remember to slide
both sleeves onto the cable before you make the loop. Determine how long
you want the madeup cable to be. Mark the cable length with the Sharpie.
That mark is the outside end of the second loop. Proceed to build the
second loop as described above.
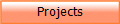 |